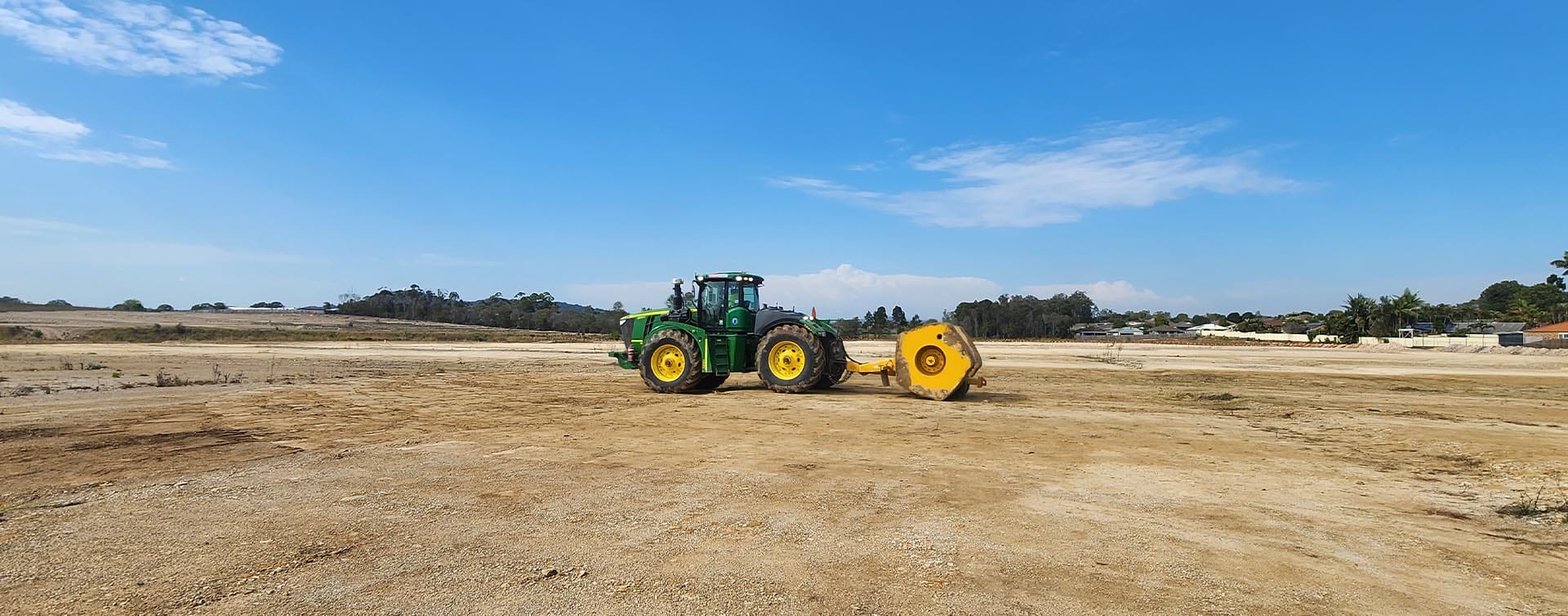
Understanding High Energy Impact Compaction (HEIC)
High Energy Impact Compaction (HEIC) revolutionises ground improvement with its ability to achieve superior soil density and stability. Unlike traditional methods, HEIC uses advanced rollers and compaction technology to penetrate deeper soil layers.